How much does it actually cost to build a car
Do you know how much it actually costs to build a car? Believe it or not, the actual cost of building your own car is going to vary a lot depending on what car you build, where you are building it, the type of materials and parts that you use, and the level of professionalism that goes into building your car.

How much does it actually cost to build a car
The answer depends on the manufacturer, but there are some general trends we can look at.
Toyota Corolla
The Toyota Corolla is one of the most popular cars in the world, with more than 40 million sold from 1966 to 2018. Let’s take a look at how much it cost to build a Toyota Corolla over time:
The first Corolla came out in 1966, and it cost $1,368 (about $12,000 today). That’s a lot less than the current model ($20,000+).
In fact, Corollas were always relatively affordable compared to other vehicles on the market. In 1983, they were priced around $10k — which is still much cheaper than today’s models!
How much does it actually cost to build a car?
If you’re asking how much it costs to build a car, the answer is: a lot. The average price of a new vehicle in the U.S. is about $33,500, but the cost of manufacturing that vehicle can be as high as $60,000 depending on which make and model you buy.
Of course, the price tag doesn’t include things like research and development, marketing or interest on borrowed money — all of which add up to about $1 billion per year for automakers such as Ford Motor Co., General Motors Co. and Toyota Motor Corp.
The following breakdown shows how much goes into making your vehicle:
The cost of building a car is about $12,000 for the Ford Focus, $10,000 for the Toyota Corolla and $30,000 for the Tesla Model S.
The cost of producing a new car has been steadily increasing over the past decade. In 2010, it cost an average of $8,500 per vehicle. By 2014, that average had increased to $9,300 per vehicle. In 2016, it was up to $10,600 per vehicle.
The price tag includes direct materials costs, which are materials purchased directly from suppliers such as steel or plastic; direct labor costs; and manufacturing overhead costs such as indirect labor and administrative expenses like office rent.
The cost to manufacture a car is a complicated equation that can be broken down into three main parts: materials, labor and overhead.
Materials include the cost of the steel and aluminum required to build the body frame, as well as any other components made from plastic or rubber. Some materials are purchased directly from manufacturers, while others are bought through vendors who then purchase them from their own suppliers. Labor includes all wages paid to employees who assemble vehicles on assembly lines. Overhead includes indirect costs such as rent and utilities, as well as administrative expenses such as office supplies and employee benefits.
In addition to these three major categories, there are other costs that don’t fall neatly into one category or another but still contribute significantly to total manufacturing costs. These include marketing expenses such as advertising campaigns and incentives for dealerships to sell cars; shipping costs from supplier locations; insurance against damage during shipping; warranty coverage for vehicles sold; taxes paid by manufacturers on their profits (or losses); interest paid on loans used for capital investments such as new production facilities or equipment upgrades; and depreciation of assets used in manufacturing (such as factory buildings).
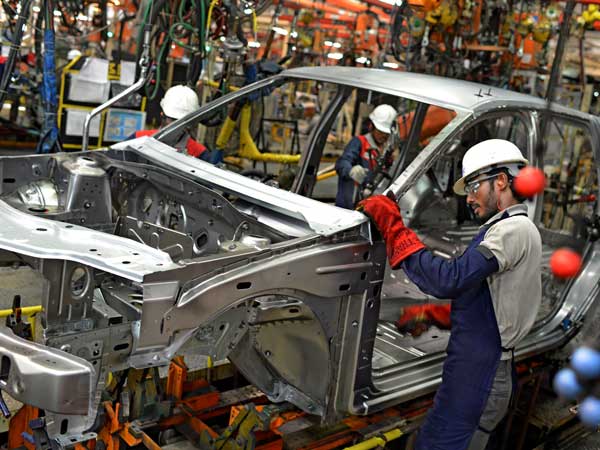
How much does it actually cost to build a car?
The cost of building a car is astronomical. The average price tag for an automobile in the U.S. is $36,000, but that figure doesn’t include the cost of research and development, manufacturing costs or marketing expenses. While there’s no direct answer to “how much does it cost to build a car,” there are some factors that can help us get closer to the answer.
Research and Development
Car companies typically spend millions of dollars researching and developing new models before they go into production. They also invest heavily in testing prototypes at high speeds on test tracks and on public roads. A good example of this is Tesla Motors’ Model S sedan model which took about five years to develop at a cost of over $200 million dollars! This investment helps ensure that each new model meets safety standards set by regulators around the world, as well as performance requirements set by each company’s engineers.
How much does it cost to make a car?
The answer depends on which company you ask.
Toyota, for example, says it costs $15,000 per Corolla. Ford says it costs $8,300 to build a Focus sedan. And GM claims it spends $2,600 per Chevy Sonic hatchback and $40 per Spark minicar.
These are just estimates — no one really knows how much it costs to manufacture a car. What we do know is that the price of an average vehicle has steadily increased over the past decade while labor costs have remained relatively flat (thanks in part to automation). This means that manufacturers must be spending more on parts than ever before — and that means higher sticker prices at dealerships across the country.
The following list breaks down some of the biggest expenses associated with building one of America’s most popular vehicles:
Toyota Corolla has been in production since 1966, but the current model was introduced in 2011. The Corolla is one of the most popular cars in the world, with over 40 million units sold since its launch.
Toyota manufactures around 4,000 engines per day and produces around 1 million cars every month globally. The company also manufactures many other components internally as well. It’s hard to say exactly how much it costs Toyota to manufacture a car because there are so many factors involved – from the cost of raw materials to labor costs, taxes and other expenses involved in producing a vehicle.
Toyota makes two versions of the Corolla: one for North America (1AZ-FE) and one for Europe (1NR-FE). Both engines are four-cylinder 1.8-liter units that use direct injection technology and produce either 122 horsepower or 140 horsepower depending on options selected by the customer.
Car manufacturing costs are about $4,000 per vehicle. The costs include materials and labor.
The average cost of a car is about $34,000, but there are many factors that affect the price. The most expensive part of a car is the engine. The cost of a new engine varies depending on the type of car and whether it’s an import or domestic model. A new engine in a Toyota Corolla or Honda Civic costs around $3,000 to $5,000 each.
Other major components include tires, brakes and battery packs. Each component has its own price range depending on brand and type. For example, a set of new tires for a Ford Focus costs between $300 and $600 while the same tires for an Audi A5 can be as much as $1,200 per tire set!
The cost of manufacturing a car is made up of many different factors. It can be hard to get an accurate estimate of how much it costs to manufacture a car because the cost depends on what class the car is in and what kind of features it has.
The first step in determining how much it costs to manufacture a car is figuring out how much each part costs. For example, if you’re making a Ford Mustang, then you need to know how much each part costs for that particular model.
Once you have all the parts figured out, multiply them by their quantity and add them together. This will give you an estimate of how much it would cost to manufacture your Ford Mustang from start to finish.
Now that we know how much it costs to manufacture our Ford Mustang, we need to figure out how much profit there will be from selling one unit of this car at retail price.
To do this, we need to take into account all the expenses that go into making each unit and then adding those costs onto our total manufacturing cost (total parts multiplied by quantity). This gives us our final retail price per unit which we’ll use as our profit margin percentage when calculating advertising costs later on in this article
How much does it cost to make a car?
The short answer is that it varies. The more you know about the car you’re building, the more accurate your estimate can be. The first step is to identify which parts of the car will be made in-house (engine, transmission) and which ones will be outsourced (body panels, tires). Then you can break down each component into its own cost category: raw materials, labor, equipment and overhead. Once you have all of those numbers together, add them up to get an estimate of how much it costs to make one unit of whatever product you’re making.